CNC foam cutting machine
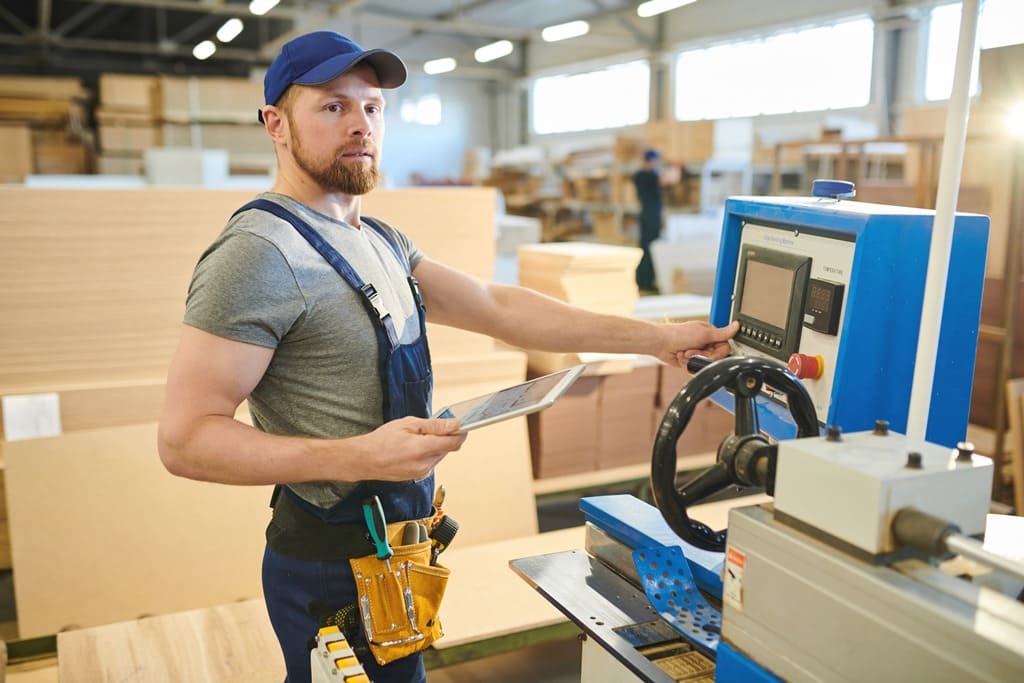
Are you looking for a way to streamline your foam cutting process and increase efficiency in your business? Look no further than the CNC Foam Cutting Machine. In this article, we will provide an introduction to this innovative technology, including how it works and the types of foam materials it can cut. We’ll also guide you through choosing the right machine for your business and highlight the benefits of using one. Additionally, we’ll offer maintenance and troubleshooting tips to keep your machine running smoothly. Finally, we’ll explore advancements and trends in the industry that point towards a bright future for CNC Foam Cutting Machines. Keep reading to learn more!
CNC Foam Cutting Machine
CNC foam cutting machines are a type of computer-controlled equipment that is used to cut foam materials into various shapes and sizes. These machines use advanced software programs to control the movement of the cutting tool, which allows for precise and accurate cuts every time. CNC foam cutting machine is widely used in a variety of industries, including packaging, automotive, aerospace, and construction.
The basic principle behind CNC foam cutting machines is simple: they use a hot wire or blade to cut through foam materials. The machine’s software program controls the movement of the wire or blade, allowing it to follow a pre-determined path and create complex shapes with ease. The operator simply inputs the design into the software program, and the machine takes care of the rest.
CNC foam cutting machines are becoming increasingly popular in the manufacturing industry due to their precision and efficiency. These machines use computer-controlled technology to cut foam materials into specific shapes and sizes with ease. The foam cutting process is essential for a wide range of industries, including automotive, aerospace, and packaging.
The CNC foam cutting machine works by using a hot wire or blade to cut through the foam material. The computer program controls the machine’s movements to ensure that the cuts are precise and accurate. This technology allows for complex shapes and designs to be created quickly and efficiently, saving time and reducing waste. The foam cutting process can also be automated, further increasing efficiency and reducing labor costs. Overall, CNC foam cutting machines are a valuable asset for any manufacturing facility looking to improve productivity and accuracy.
A CNC foam cutting machine is a computer-controlled cutting device that is specifically designed to cut foam materials into different shapes and sizes. It uses a high-speed rotating tool to cut through the foam, which is held in place by a vacuum table. The cutting process is controlled by a computer, which reads the design file and translates it into a set of instructions that the machine can follow.
The basic principles of a CNC foam cutting machine are relatively simple. The machine consists of a cutting tool, a vacuum table, and a computer control system. The cutting tool is mounted on a gantry that moves along the X, Y, and Z axes, allowing it to cut foam in three dimensions. The vacuum table holds the foam in place during the cutting process, ensuring that it remains stationary while the cutting tool moves.
There are several key components that make up a CNC foam cutting machine. These include the cutting tool, the gantry, the vacuum table, and the computer control system.
The cutting tool is typically a high-speed rotating blade or wire that is used to cut through the foam material. The blade or wire is mounted on the gantry, which moves it along the X, Y, and Z axes to cut the foam in three dimensions.
The gantry is the mechanism that supports the cutting tool and allows it to move along the X, Y, and Z axes. It is typically made of aluminum or steel and is designed to be rigid and precise.
The vacuum table is used to hold the foam material in place during the cutting process. It is typically made of aluminum or steel and is perforated with small holes that allow air to be drawn through the table and hold the foam in place.
The computer control system is the brain of the CNC foam cutting machine. It is responsible for reading the design file and translating it into a set of instructions that the machine can follow. The control system also monitors the cutting process and makes adjustments as necessary to ensure that the foam is cut accurately and efficiently.
Overall, a CNC foam cutting machine is a powerful tool that can be used to cut foam materials into a wide range of shapes and sizes. By understanding the basic principles and key components of the machine, users can make the most of this technology and create precise, high-quality foam products.
One of the key advantages of CNC foam cutting machines is their ability to produce consistent results. Unlike manual cutting methods, which can be prone to human error and inconsistencies, CNC foam cutting machines are highly accurate and reliable. This makes them ideal for producing large quantities of identical parts or products quickly and efficiently.
CNC Foam Cutting Machine - materials
When it comes to CNC foam cutting machines, one of the most important factors to consider is the type of foam materials that can be cut. Fortunately, these machines are incredibly versatile and can handle a wide range of foam materials with ease.
One common type of foam material that can be cut with a CNC foam cutting machine is expanded polystyrene (EPS) foam. This lightweight and durable material is often used in packaging, insulation, and construction applications. With a CNC foam cutting machine, you can easily create custom shapes and designs from EPS foam for your specific needs.
Another popular type of foam material that can be cut with a CNC foam cutting machine is polyurethane (PU) foam. This flexible and resilient material is commonly used in furniture cushions, automotive interiors, and soundproofing applications. With a CNC foam cutting machine, you can quickly and accurately cut PU foam into any shape or size required for your project.
CNC Foam Cutting Machine - How to Choose the Right
When it comes to choosing the right CNC foam cutting machine for your business, there are several factors that you need to consider. First and foremost, you need to determine the type of foam materials that you will be cutting. This will help you narrow down your options and choose a machine that is specifically designed for the type of foam material that you work with.
Another important factor to consider is the size of the machine. You need to make sure that the machine can accommodate the size of foam blocks or sheets that you typically work with. Additionally, you should also consider the cutting speed and accuracy of the machine, as well as its overall durability and reliability.
Finally, it’s important to consider your budget when choosing a CNC foam cutting machine. While it may be tempting to go for a cheaper option, investing in a high-quality machine can actually save you money in the long run by reducing downtime and maintenance costs. Be sure to do your research and compare prices from different manufacturers before making a final decision.
CNC Foam Cutting Machine - benefits
Using a CNC foam cutting machine can bring numerous benefits to your business. One of the most significant advantages is the precision and accuracy that this machine offers. With its computer-controlled system, you can cut foam materials with high precision, ensuring that each piece is identical to the next. This level of consistency is essential for businesses that require uniformity in their products, such as those in the packaging or insulation industry.
Another benefit of using a CNC foam cutting machine is its speed and efficiency. Compared to traditional methods of cutting foam materials, such as manual cutting or sawing, a CNC foam cutting machine can produce more pieces in less time. This means that you can increase your production rate and meet your customers’ demands faster without sacrificing quality.
Moreover, using a CNC foam cutting machine can also help reduce material waste. Since the machine follows a pre-programmed design, it cuts only what is necessary, minimizing scrap materials and saving you money in the long run. Additionally, this eco-friendly approach aligns with today’s sustainability efforts and can improve your business’s reputation among environmentally conscious consumers.
Maintenance and Troubleshooting Tips for Your CNC Foam Cutting Machine
Regular maintenance of your CNC foam cutting machine is essential to ensure its longevity and optimal performance. Here are some tips to keep your machine in top condition:
Firstly, make sure to clean the machine regularly. Dust and debris can accumulate on the cutting wires, which can affect the quality of cuts. Use a soft brush or compressed air to remove any dirt or debris from the machine’s components. Additionally, lubricate the moving parts of the machine with oil or grease as per manufacturer’s instructions.
If you encounter any issues with your CNC foam cutting machine, it is important to troubleshoot them immediately. One common problem is wire breakage during cutting. This can be caused by various factors such as incorrect wire tension, worn-out wires, or improper alignment of the wire guides. Check these components regularly and adjust them as needed to prevent wire breakage.
Future of CNC Foam Cutting Machine: Advancements and Trends in the Industry
The future of CNC foam cutting machines is bright, with advancements and trends in the industry that promise to make these machines even more efficient and effective. One trend that is already making waves is the use of artificial intelligence (AI) in CNC foam cutting machines. With AI, these machines can learn from their past performance and adjust their settings to optimize their performance for each new job.
Another trend that is gaining momentum is the integration of 3D printing technology into CNC foam cutting machines. This allows for even greater precision and accuracy when cutting complex shapes and designs. Additionally, it opens up new possibilities for creating custom molds and prototypes quickly and easily.
Finally, there is a growing focus on sustainability in the foam cutting industry, with many manufacturers looking for ways to reduce waste and minimize their environmental impact. As a result, we can expect to see more eco-friendly materials being used in foam cutting processes, as well as innovations in recycling and repurposing foam waste.
Autor: Materiał partnera